For homeowners seeking to upgrade their garages with professional flooring, sealing in long-wearing epoxy coatings enhances aesthetics while delivering protective performance. When properly self-installed or contracted out to specialists like Speedway Flooring, applying these commercial epoxy coatings as liquid layers ultimately cures into durable, resilient floor surfaces ideal for demanding shop environments.
However, careful preparation before laying epoxy, using compatible application tools, selecting quality commercial products suitable for garage use, and limiting environmental factors during the curing window all determine lasting success. Follow these best practice insights for securing a high-functioning, protective garage epoxy floor finish built to handle tough workshop conditions now and well into the future.
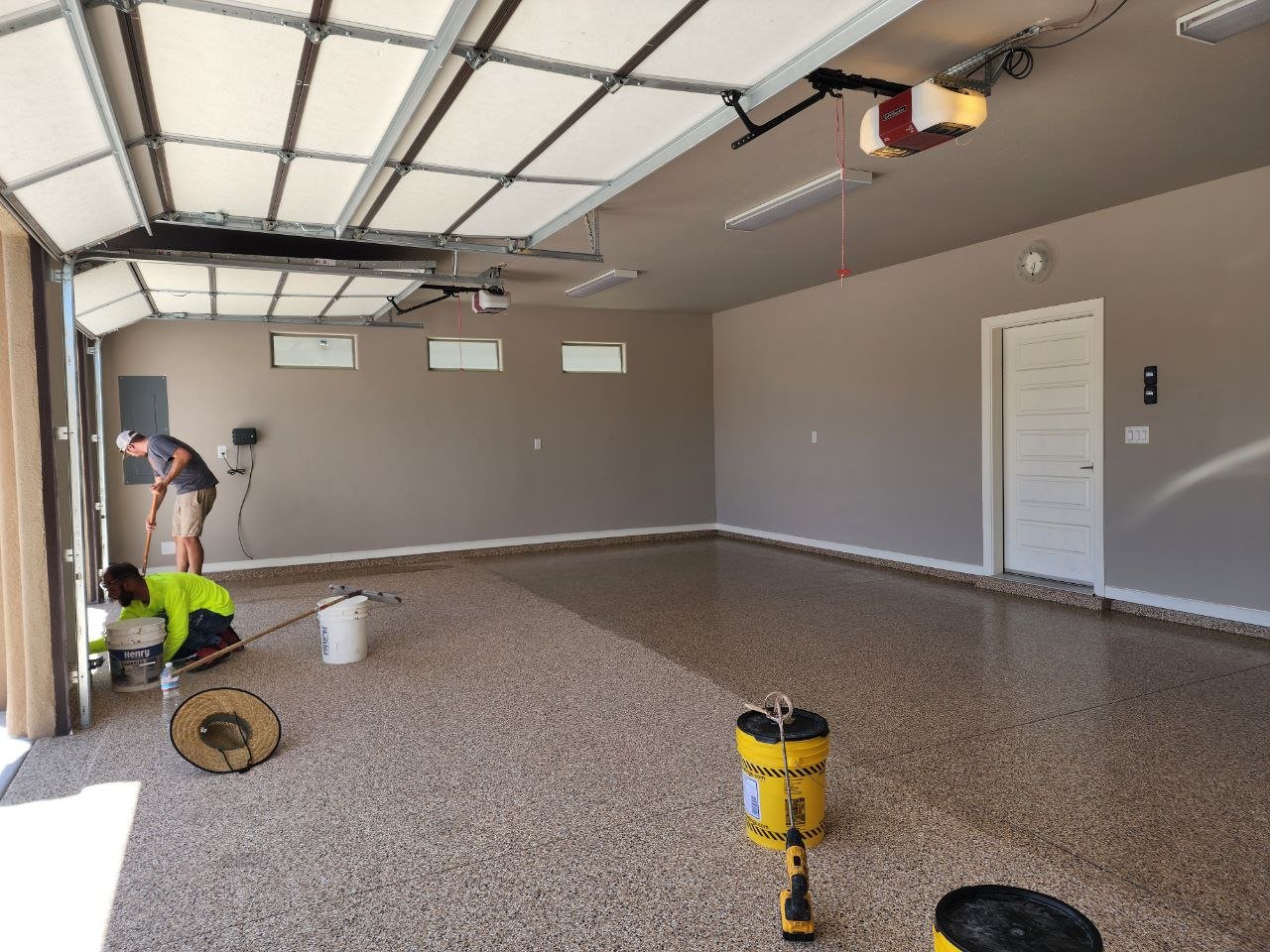
Choosing Commercial Grade Floor Coatings
Home improvement stores offer various enamel paints, stains, or thin sealers for garage floors targeted at casual household use. But for areas seeing heavier traffic, constant vehicle parking, potential chemical contact, or other commercial demands, rely instead on dedicated commercial epoxy solutions thickly applied that excel at handling abuse after full curing. These stronger formulations also resist staining, inhibit slickness, and minimize concrete dusting from bare floors.
The best commercial epoxy floor coatings are:
-
Solvent-cured—Offer stronger crosslinking as carrier fluids evaporate fully once spread onto the slab, rather than lower VOC water-based varieties.
-
100% solids content—Higher thickness coverage from complete reactive resins for greater durability without thinning additives.
-
Polyaspartic chemistry—Fast-curing epoxy variant for quicker project timelines by certified applicators.
Generally, thick 100% epoxy solutions deliver adequate coverage in two coats, while thinner paint formulas require three. Consult reputable manufacturers like Sherwin-Williams, Dow Chemicals, or PPG to select the right commercial brand meeting quality assurance spec for rigorous demands. Contract installers offer the right selections.
Floor Preparation—Cleaning & Repairs
Before applying high solids epoxy coatings to cement for maximum adhesion durability, thoroughly clean then inspect and fix the existing slab foundation ensuring soundness.
-
Pressure wash the entire surface using degreases to penetrate oily grime if present
-
Check for smaller cracks and holes needing patching compound fillers drying completely
-
Assess moisture content that dictates suitable products for damp tolerance
Preparation also requires testing if existing enamels or paints risk compatibility barriers, impeding proper bonding. Window 24 hours ensuring bone dryness for epoxy spreading best across a uniformly profiled surface.
Employing Correct Tools and Techniques
Applying commercial-quality thick resins requires working efficiently before slower drying windows expire especially for larger square foot jobs. Maintain ideal temperature ranges. Use correct application tools and techniques suited to each coating including:
-
Flat squeegees spread initial primer/base layers evenly
-
Non-shedding roller covers for secondary self-leveling top coatings
-
Stiff concrete brooms for smoothing viscous coats
-
Paintbrushes reach corner joints and crevices adequately
Installers also wear spiked shoes walking newly laid epoxy spreads to release trapped air pockets or drag custom loop roller tools texturing anti-slip profiles like shark grip patterns once sections cure initially. Carefully follow manufacturer technical guidelines for best results.
Limiting Early Environmental Factors
As vulnerable reactive compounds applied across the floor begin chemically curing, several ambient factors can hinder hardening properly:
-
Temperature extremes either too hot or freezing cold
-
Standing liquids or condensation accumulating on the floor
-
Dust particle debris settling into still-tacky layers
-
Any physical contact before sufficient drying occurs
Shield garage doors to prevent drafts during application. Dehumidify the concrete prior and avoid morning/evening times prone to condensation. Install signs marking freshly coated zones clearly designating no entry for 24-48 hours until achieving handling cure minimums. Being disturbed early risks epoxy bonding integrity. Patience pays off.
Expected Cost Projections
In general epoxy floor coating costs range $4-$8 per square foot depending on factors like:
-
Number of mils thickness needed for durability aims
-
Square footage size driving labor and material quantities
-
Type of chemical resistant, commercial-grade product specified
-
The amount of slab preparation involved correcting flaws beforehand
-
Optional preferences like color tints, logos, artistic designs, or traction additives
-
Regional contractor supply rates which calculate travel fees
Collect detailed quotes from experienced installers specializing in high-grade epoxy flooring carrying all bonding agents, properly calibrated equipment, and insured staff to deliver correctly. Consider warranties ensuring quality application workmanship supporting improved garage floor finishes for future years of service relaxing indoors.